Submitting a PCB: The Cool Off Period and other Techniques
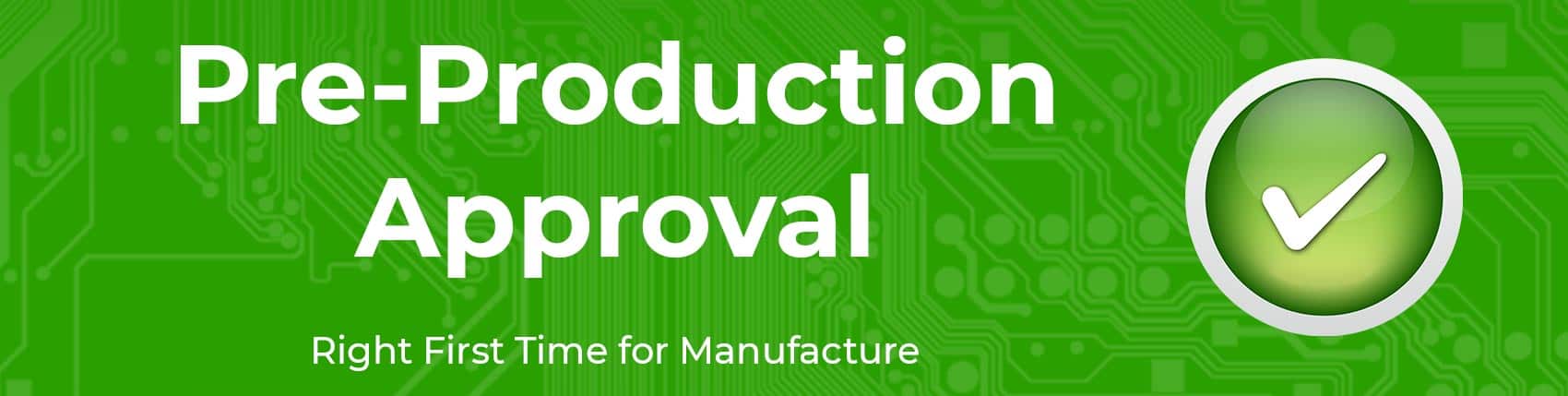
Pressing the button to submit a board for manufacture is a major event in the life of a PCB designer; it’s the culmination of days or months or years of work. After submitting the board we can relax… but inevitably the anxious feeling of having done something wrong creeps in. Many of us have experienced, I’m sure, waking up in the middle of the night with the realisation that there is indeed a mistake, rushing to the computer to see if we can cancel the job! There are several things that can help us discover issues before we submit, and there’s even one for after that.
To reduce mistakes, delays, and possible re-spins, understanding the manufacturing capabilities of the fab we’ll be using is important. A first step is to set up our tool’s design rule checks (DRC) so that we can verify our design against the capabilities of our manufacturer or a standard we’ll both be using.
At some point we lose the real dimensions of the PCB because we’ve viewed it zoomed-in for so long. Viewing the design in different environments is therefore a good idea. A Gerber viewer gives us two things here. Firstly, the Gerbers are closer to the manufacturing data. And secondly, the viewer normally has a different colour scheme, which sometimes makes mistakes pop out. Any fresh look at the design in a different environment than the one we normally use is quite helpful; it resets our blind spots caused by staring at something for a long time. We can also get fresh eyes by asking others to look at the design, or taking long breaks between views.
While some tool packages do full mechanical integration, for those who have them and for those who don’t, I’d recommend printing the board at 1:1 scale on a piece of paper. This gives us two things. Firstly, for the first time we can see the board’s actual dimensions so something obviously wrong may just stare back at us. Secondly, we can do a ‘dry’ fit with actual components to verify tolerances and footprints. (I’ve always made an effort to have samples of all the components I’m using before submitting the board just for this exercise.) It’s much easier to notice problems such as clearances between connectors this way — can a torque wrench fit between these SMAs? — compared with doing the same on the screen.
After all that you can upload the design to Eurocircuits’ Visualizer for another fresh view and a manufacturing analysis that’s independent of your design software and one that is tuned to the Eurocircuits’ manufacturing capabilities. We call it Virtual Manufacturing. If all is well there we can submit the board. Yay!
A final save beyond the launch
But Eurocircuits has another ‘trick’ to help us, and it’s the ‘Pre-Production Approval’ (PPA) feature!
You see, all PCB manufacturers modify your design data to fit their manufacturing process and minimise manufacturing problems. They do things like maintain silkscreen clearance, fill tiny gaps in the copper, or add break-tabs. It’s normally a good thing. If they think that the change won’t affect the functionality they proceed. If there’s a chance that it might affect functionality, they should — as Eurocircuits does — let you know so that you could approve that change before proceeding. With Pre-Production Approval we are able to examine these production files just to make sure everything’s well, just before the board goals to production.
I consider the time between submission and the approval request a helpful cooling-off period. I’m now more relaxed and have had a bit of time to ‘sleep on it’. It’s an opportunity to look at the design with refreshed eyes and abort if I notice a problem. The time it takes for Eurocircuits to issue a request for approval and the time you’ll need to respond by (without a delay in the lead time) depends on the order details. If, for example, it’s a two-day lead time you’ll get a notice quickly and we’d need you to respond quickly. For a five-day turn there will be more time for both the request and approval period.
There are two ways to tell us you’d like ‘Pre-Production Approval’. You can tick the PPA box at the bottom of the Visualizer’s ‘Summary’ tab when placing an order, or select it in the ‘View running orders’ page in your account, although once the order status reaches ‘Panelise’ PPA is no longer available. Then we will let you know when the design has been fully processed so that you can approve the actual production data; we’ll send you an email and also an SMS alert if you’ve provided your phone number when placing the order.
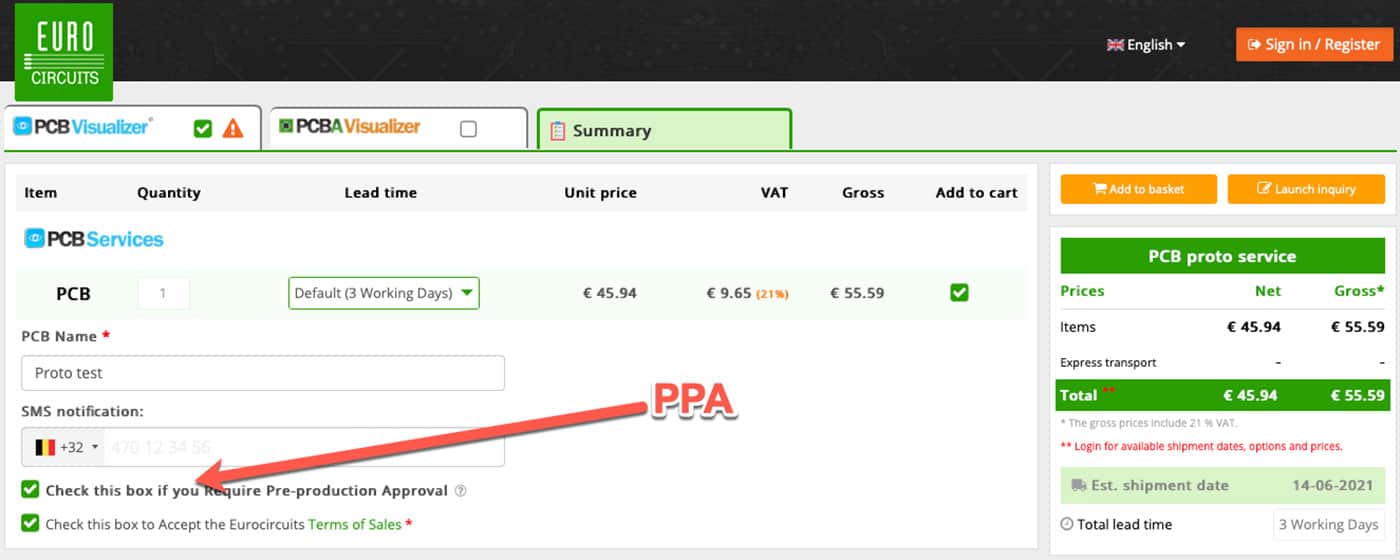
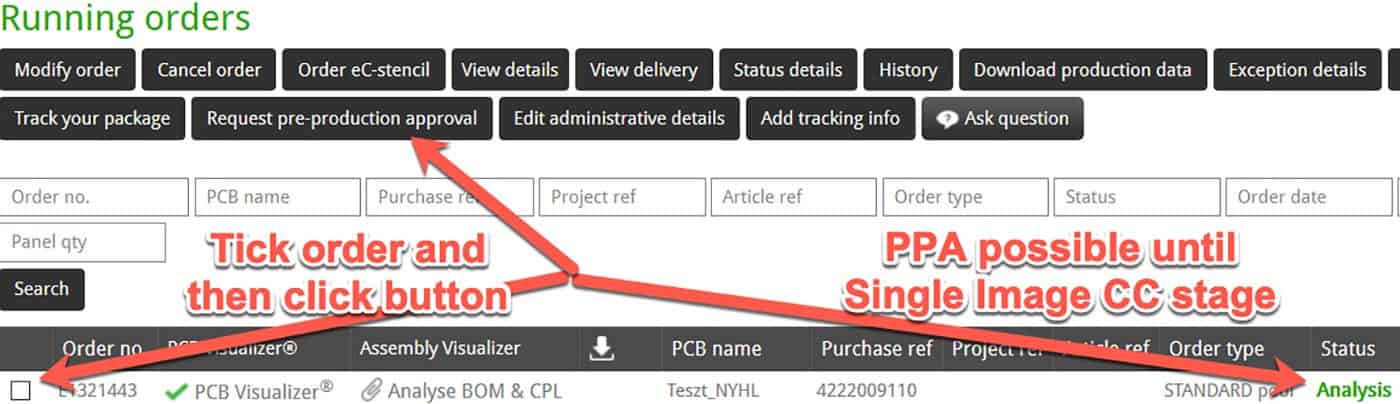
When we send you a request for approval, we have finished processing and are ready to proceed to manufacturing and deliver at the lead time you’ve selected. To keep that timeframe we suggest that you approve as soon as possible after the request. For me, even if there’s a chance for a delay in production I think that it’s worth it because it’s easier and cheaper to delay than having to pay and wait for a re-spin.