Update on fire in our Hungarian Factory (27/10/21)
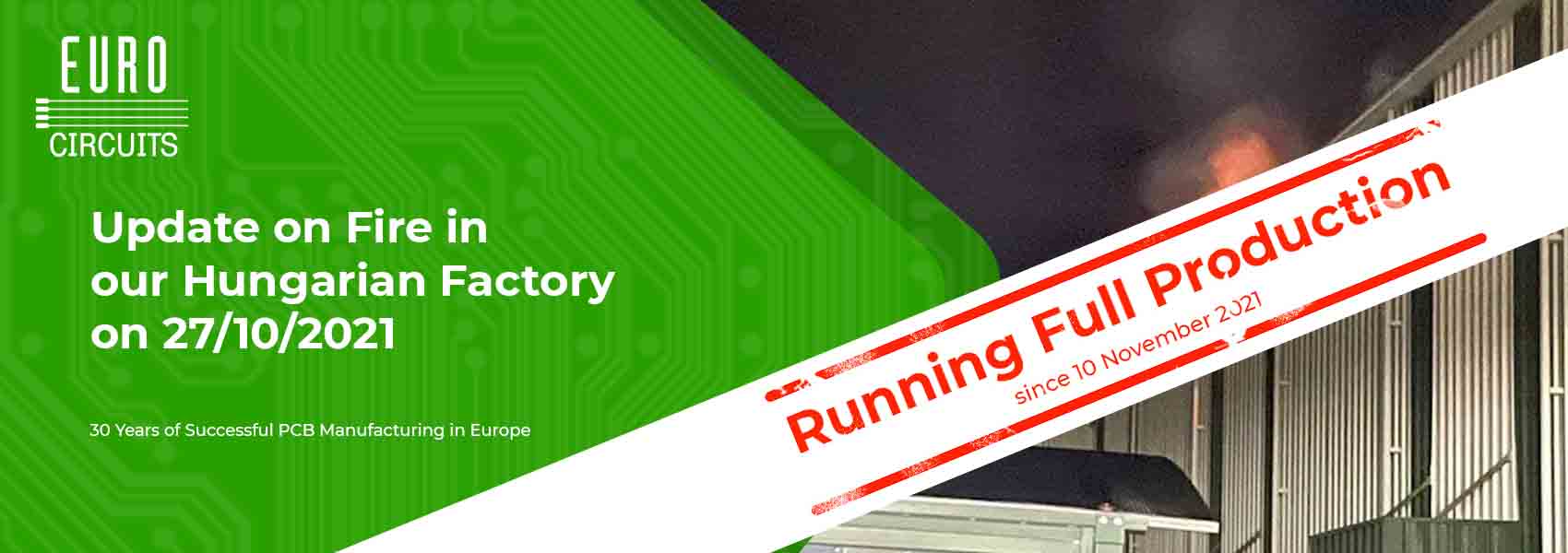
On Wednesday the 27 October 2021 we had a fire in our factory in Eger, Hungary and for the time being we must rely on the capacity of our factory in Aachen, Germany.
Our thanks to all our staff in the Hungarian factory for their response to the fire and especially to those who initially tackled it before the fire services arrived. We have one person who received minor injuries whilst tackling the fire and they are ok having received medical treatment.
Thank you for your support and understanding.
Updates
The full story reads in chronological order from bottom to top.
08/11/2021 @ 14:00 – Things are getting back to normal in the production flow
- With some exceptions, all orders that were delayed due to the disruption of the production flow by the recent fire, will be sent to customers in this afternoon’s shipment.
- We have increased our service range limitation to 500dm2 per order for double sided boards and 300dm2 for multi layers and with a total order value of 3.000€. This allows our factories to gradually get back on track during this week. If you have a need that falls outside of this, please speak to our customer service team.
- All machines and processes are running smoothly again, except for the machines that were destroyed by the fire (HAL and hard gold) for which we have organized subcontracting. This has an implication on the lead time of an additional 2 working days.
05/11/2021 @ 11:00 – Getting ready to start the next week as normal as possible
- We’ve arranged another weekend shift to clear through as many of the affected orders as possible to bring us back on track.
- The list of delayed orders is shrinking considerably: 533 orders Wednesday, 356 orders Thursday, to 150 orders this morning (Friday). We hope it will be close to zero by Monday afternoon’s order shipment.
- Assembly orders are hardly affected with delays from the PCB factory. The missing component situation is still far worse than a possible manufacturing delay of the PCB, although we give these boards priority.
We hope that from Monday on we can relax any intake restrictions in the Calculator and Visualizer, with the exception of the extra lead time we need for HAL and Goldfingers.
04/11/2021 @ 12:00 – The situation is improving dramatically and we’re working hard to clear back-logs
- We’ve arranged to subcontract the HAL and Goldfinger plating production steps, which we currently cannot do in Hungary because those specific machines were destroyed in the fire.
- The output of the Hungarian factory exceeded yesterday’s estimate: 238 orders were shipped!
- The list of delayed orders is shrinking considerably: 533 orders yesterday were reduced to 356 this morning. Clearing this list is our priority.
- Our brand-new galvanic line, installed over the summer as an extra line next to the existing one, will be started up today. This brings us to our full capacity for this manufacturing process.
We are gradually moving forward to a normal situation which we hope to achieve by the end of this week, with the exception of the extra lead time we need for HAL and Goldfingers.
03/11/2021 @ 16:00 – All processes in our Hungarian factory continue to run smoothly
Yesterday 50 newly started orders were fully processed and shipped to the customer next to orders that were already in process. Today this number has grown to 4 times that amount and we hope to report another increase in production tomorrow.
The result of the fire and the subsequent disruption of the order flow also affected the otherwise exemplary functioning of our German factory due to the factory having to fulfil both its orders and the orders in process for Hungary which requires additional flexibility of our German team. We would like to apologize for any inconvenience this delay may have caused you. Our German team is running a non-stop production to clear the ensuing back-log.
The Eurocircuits reputation is largely built on the reliability of our production flow. We are confident that we will reinstate our high service level shortly, although it will take some time to clean our building and restore everything to its original state.
02/11/2021 @ 13:00 – Saturday evening 30/10 we shut down production for the weekend after confirming that the mechanical and electrical functions of all production machines were OK
Today’s challenge is to get everything back up and running and run panels through production to evaluate and test the quality of all chemical processes.
All machines and processes are back up and running, except for the machines that were destroyed by the fire (HAL and hard gold line).
We can therefore start to release restrictions that we had placed on our services, but we need to do this in phases, as there are still many pending orders which we will of course prioritise and we do not want to cause any new bottle necks.
During the course of the day we will notify all customers that are affected by a delayed order.
So, as of this afternoon, we will start releasing restrictions and return to offering almost our full service range but for the time being limited to 300dm2 per order for double sided boards and 200dm2 for multi layers and a total order amount of 2.000€. If you have a need that falls outside of this, please speak to our customer service team.
We hope to bring you more good news in the next few days so that we can move towards a normal situation next week. In the meantime, we thank you all for your understanding in this exceptional situation.
30/10/2021 @ 11:00 – We will continue working this Saturday but during the holidays on Sunday (Halloween) and Monday (All Saints) our people will take a well earned rest.
We are very proud of what they have achieved in this short period of time, demonstrating that they are truly among the best in their field.
Getting our PCB factory back into production after being confronted with the initial situation demonstrated by the pictures below, shows enormous courage and resilience. We hope to run business as usual from next Wednesday onwards although cleaning our building and premises will take quite some time.
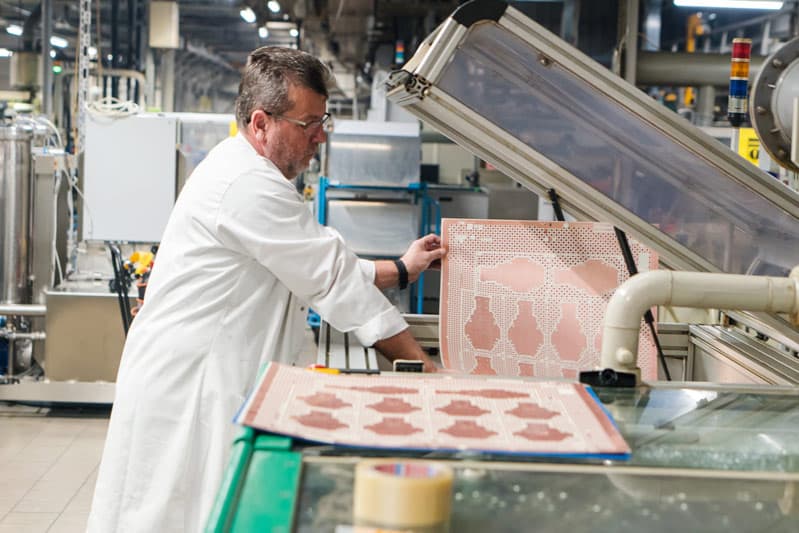
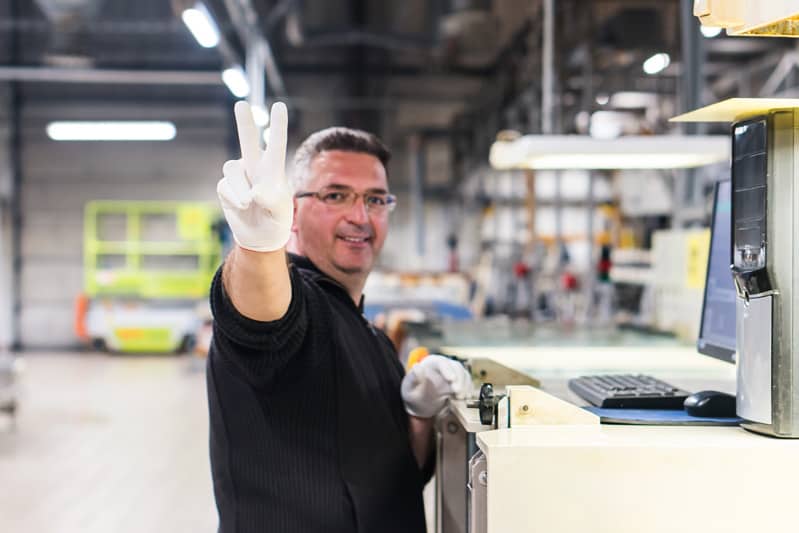
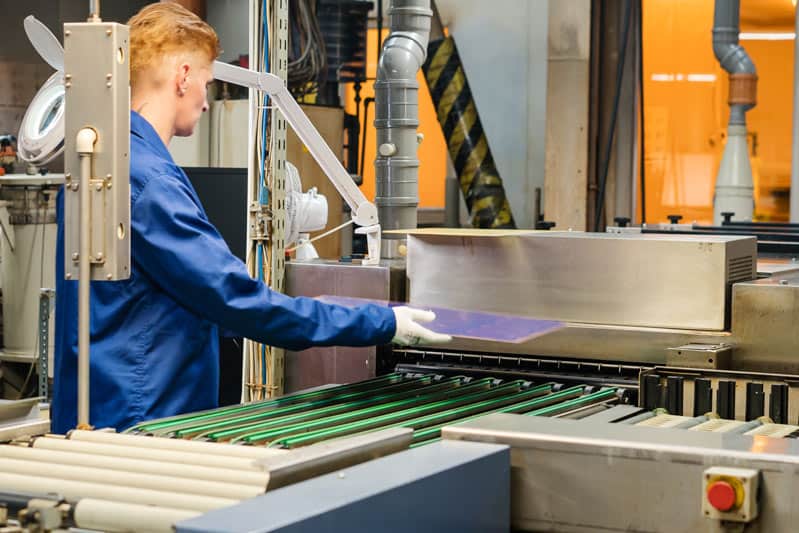
30/10/2021 @ 10:00 – The chemical gold line is up and running thus completing the full PCB manufacturing process. Eureka
This only leaves us without HAL (for which we have a back up in our German factory) and without Hard Gold line for edge connectors for which we will search for temporary help from colleagues.
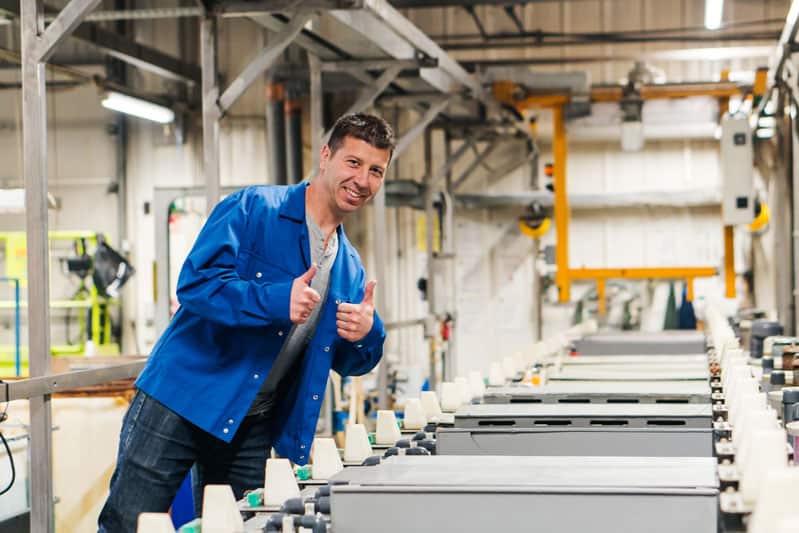
30/10/2021 @ 09:00 – Saturday morning is looking promising
- The oldest of our two galvanic lines is working at full capacity and at the required quality level.
- The new and larger galvanic line installed over the summer will need some extra work but is expected to work by the end of next week.
- 3 Ledia direct imaging machines are up and running which makes imaging for copper image and soldermask possible.
- The soldermask preparation line requires some more work but is expected to run by lunch time.
29/10/2021 @ 21:00 – Beautiful evening views from the top of our new building before going home
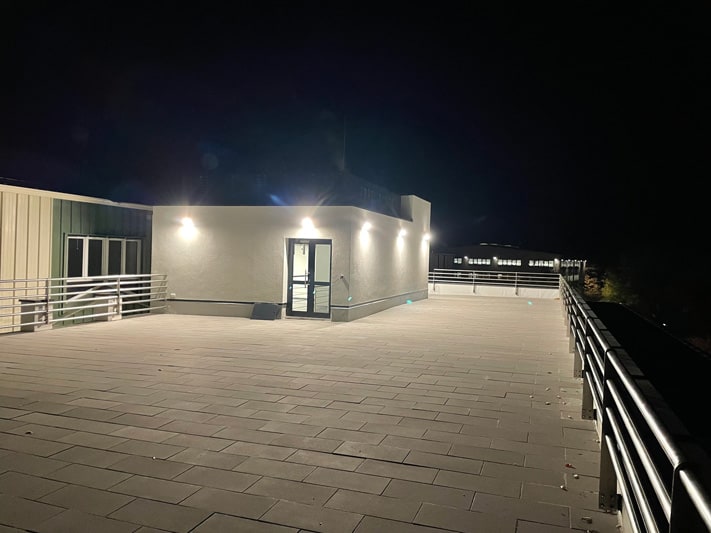
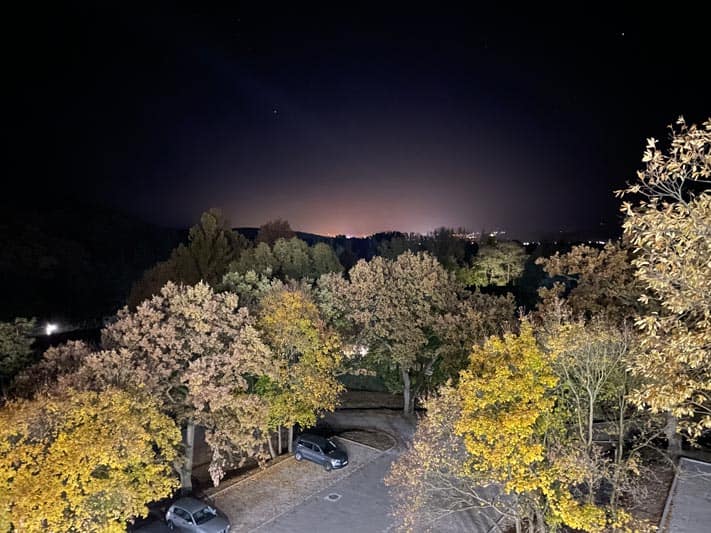
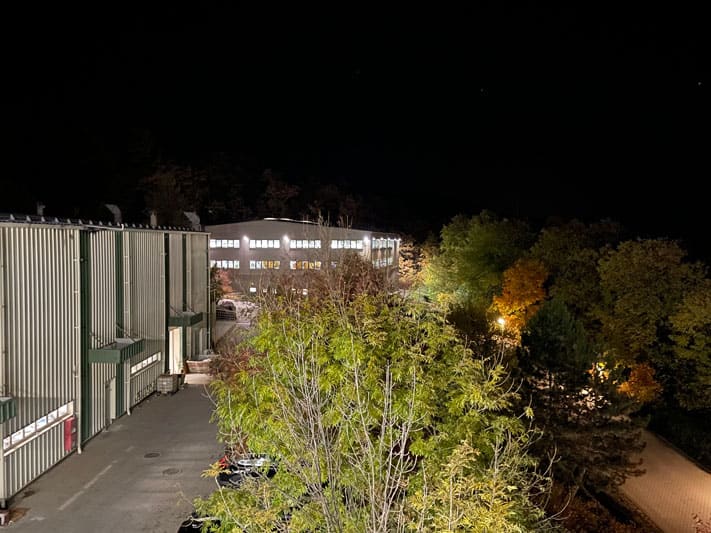
29/10/2021 @ 20:00 – Two of the 3 Ledia’s are working already so this liberates all imaging work we need
This leaves only the galvanic and the chemical nickel gold line as worry for tomorrow. Of course the HAL machines and the hard gold connector line were a total loss in the fire and must be replaced with new equipment.
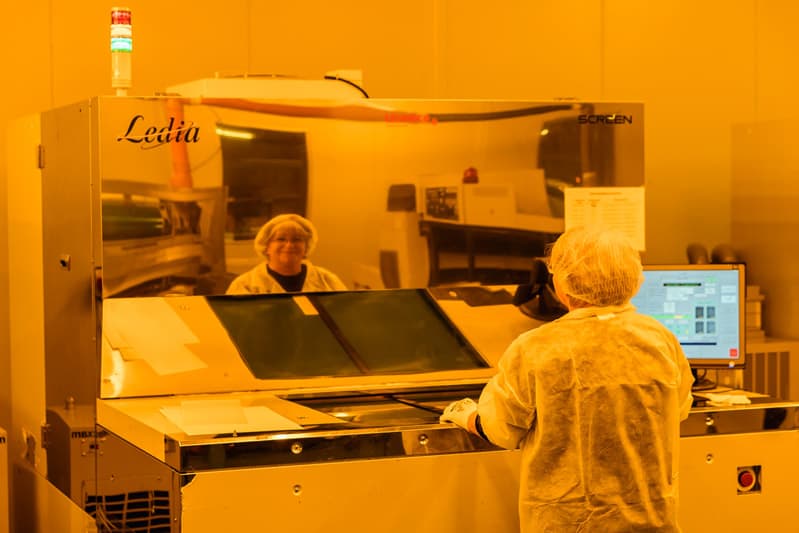
29/10/2021 @ 18:00 – Today there was again a shipment of orders to our customers and of some panels that need further processing in our Aachen factory.
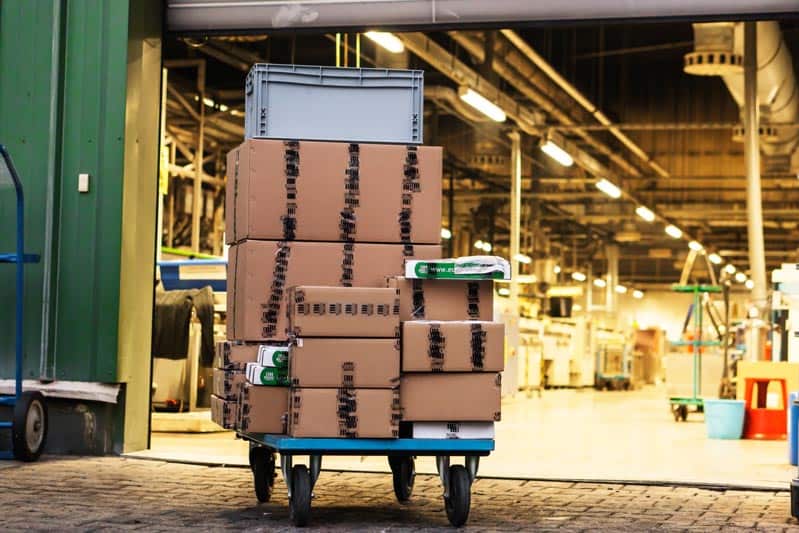
29/10/2021 @ 16:00 – The galvanic line will now run 3 test panels, one for each copper bath
After the process we can do a full quality check of the plating to determine if the plating quality is OK to start up the line for production runs. Tomorrow morning we will know more.
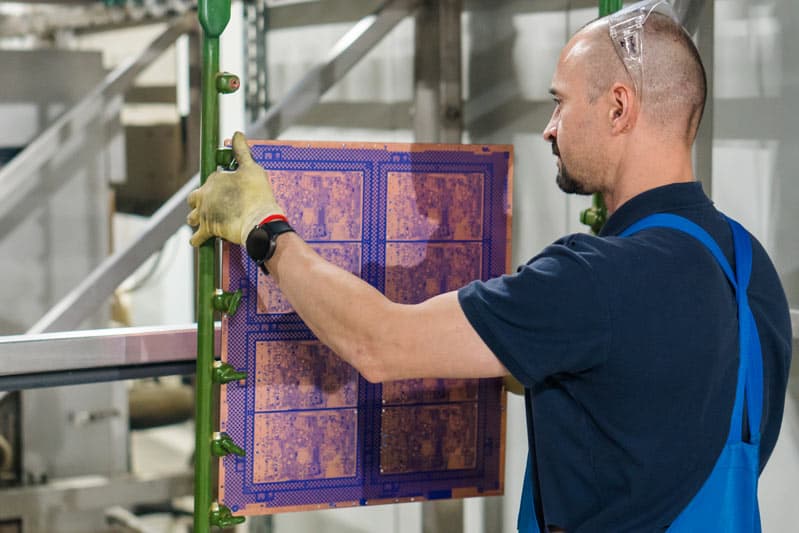
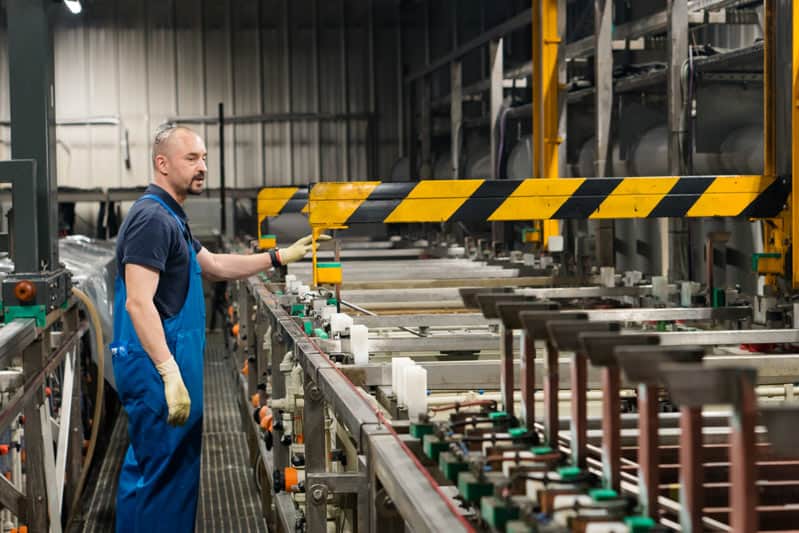
29/10/2021 @ 15:00 – The service engineer from UCAMCO arrived to inspect, clean and start up the Ledia Direct Imaging machines
We badly need those machines for imaging the copper pattern and solder mask. The engineers first impression of the situation is good and we have good hope to have our 3 machines running today.
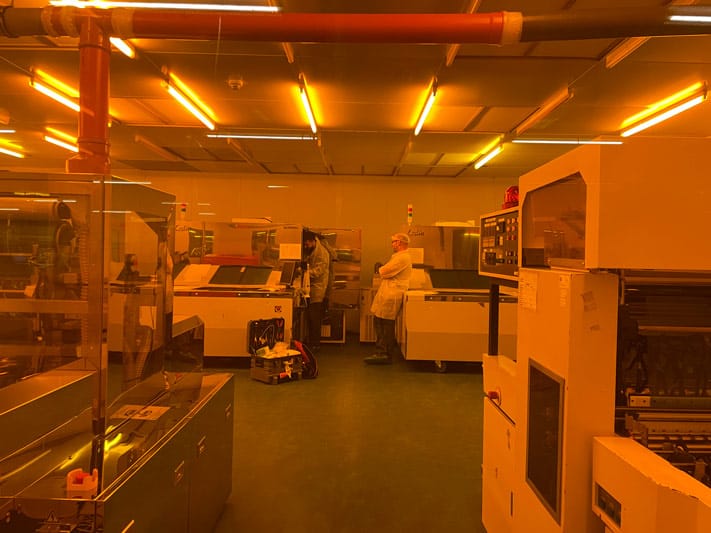
29/10/2021 @ 12:00 – Limited production started
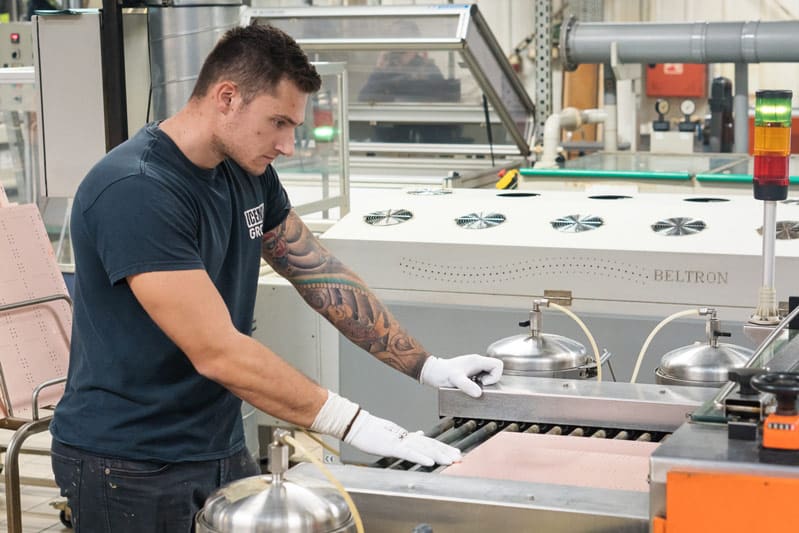
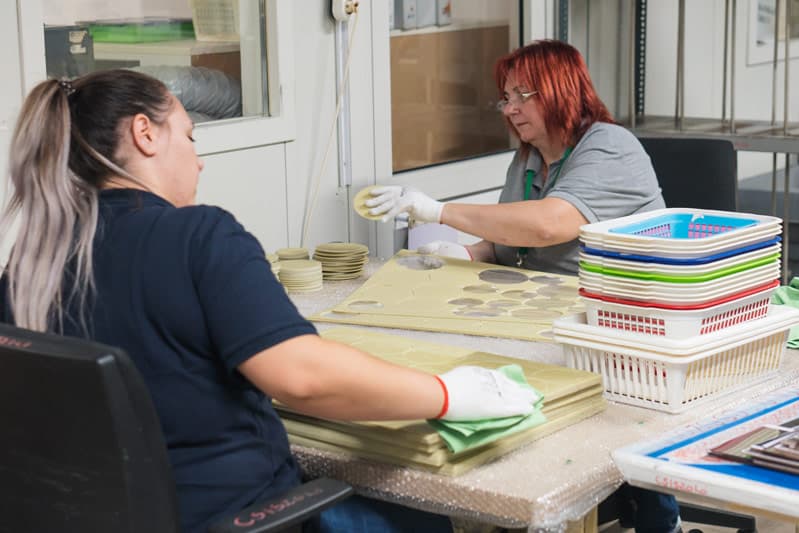
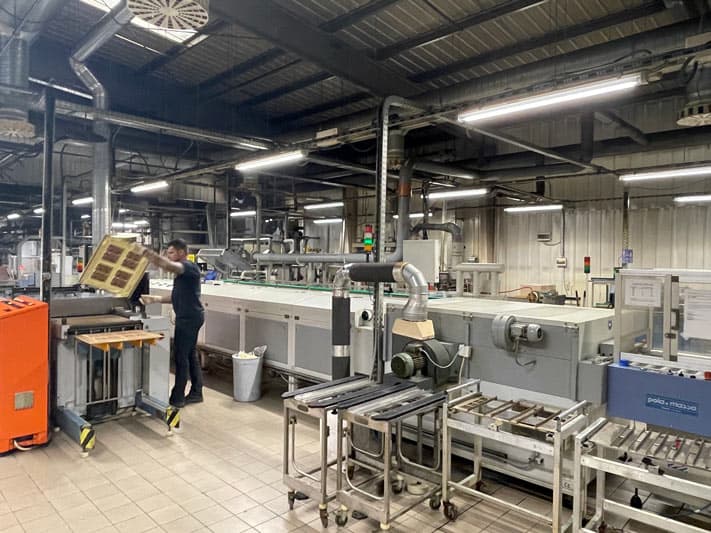
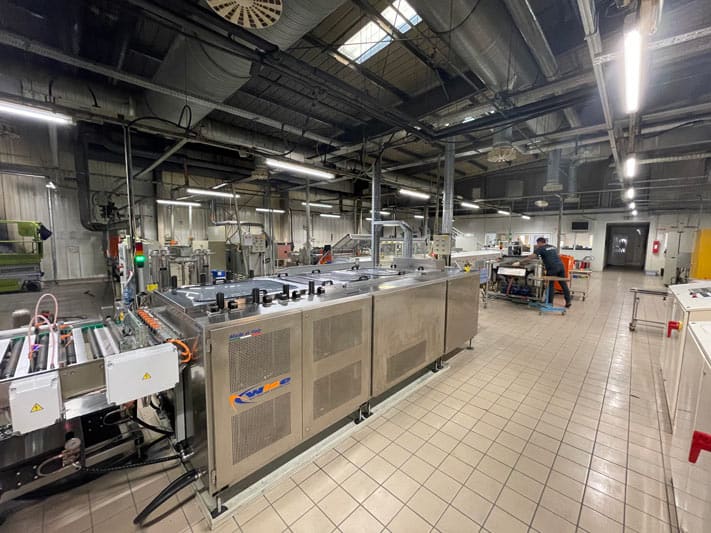
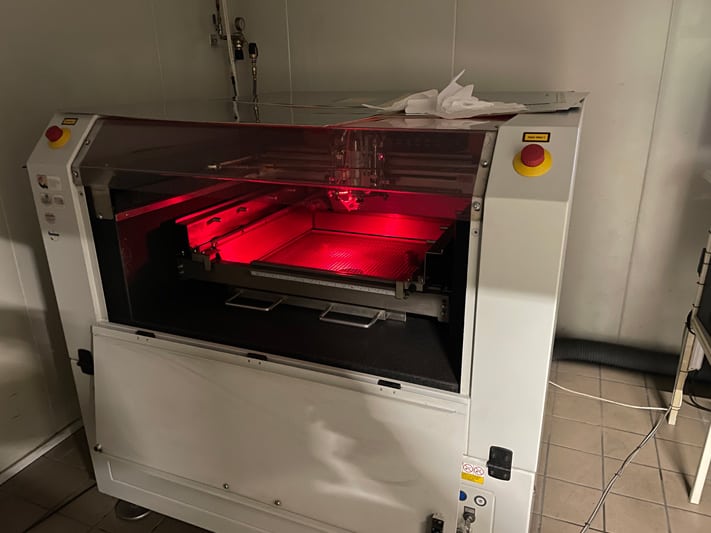
29/10/2021 @ 08:00 – The cleaning continues
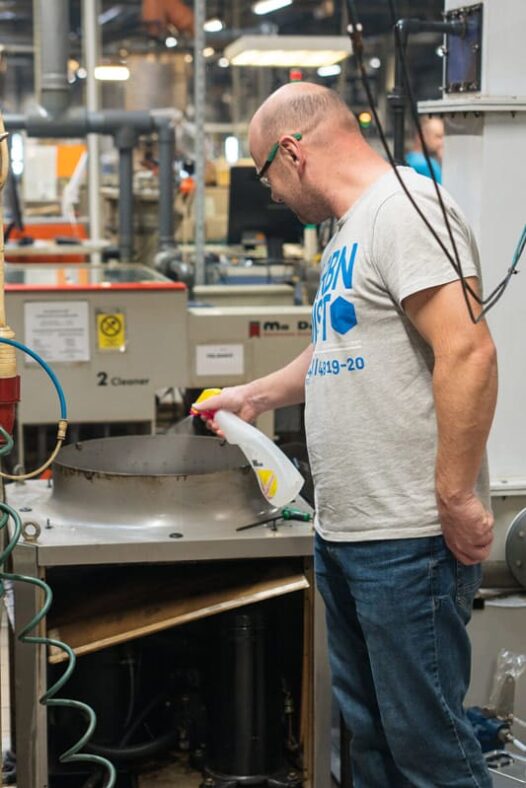
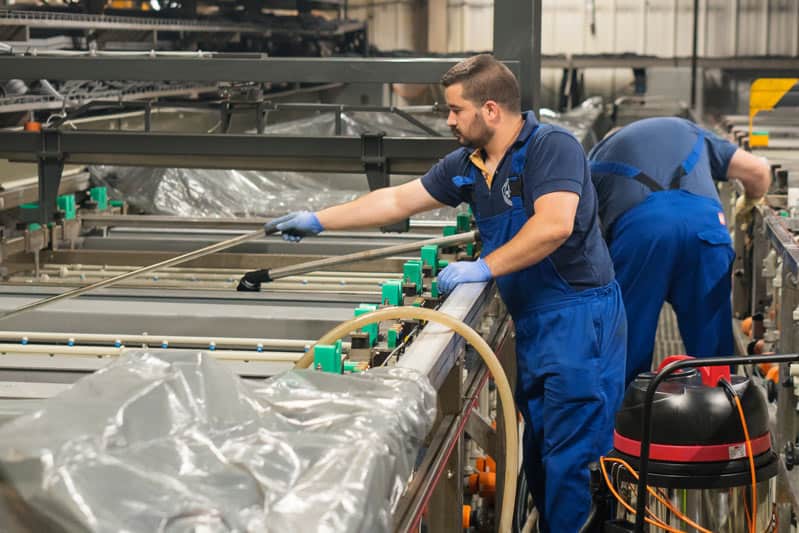
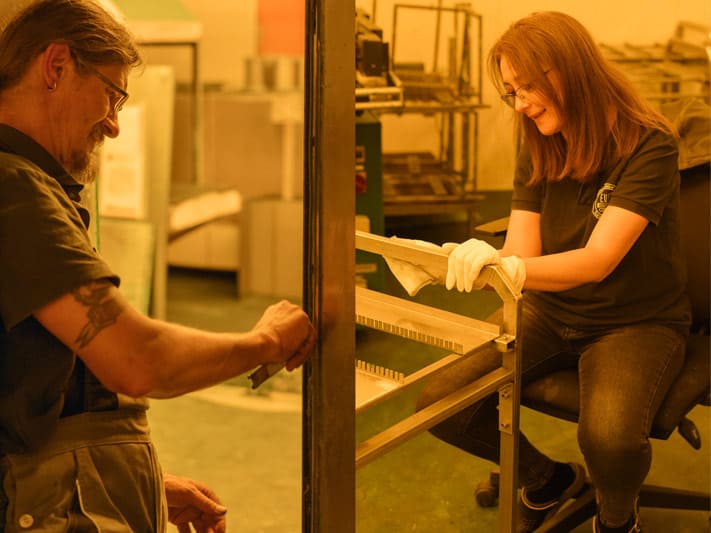
29/10/2021 – Service Update!!!
We can now offer up to 8 layers using our Standard pool service.
28/10/21 @ 23:00 – Challenge for tomorrow is
- To assess the situation of our Ledia’s laser direct imaging equipment of which we have three in operation in Eger. UCAMCO our supplier will send someone over to do this tomorrow afternoon.
- To check if we can clean the galvanic lines by filtering and rinsing. The same goes for the chemical gold line?
- Make a final assessment of the status of all running orders that might be affected by any delay.
- That’s for tomorrow, but in the meantime our night shift continues cleaning and manning those departments that are operational already.
28/10/21 @ 19:00 – More departments start their operation
- The laser cutter is cutting solder paste stencils again.
- The entire drilling and routing department is operational.
- The electrical testing department is operational.
- Digital legend printing works for colour white.
- The etching line for outer layers works.
- Most of the cleaning and micro etch machines are working.
- One ML press is working.
- Clean rooms are cleaned and up to the mark what dust is concerned.
People are hopeful and begin to see the light at the end of the tunnel.
28/10/21 @ 15:00 – More Great News!!!
Shipping orders, these were already manufactured before the fire or have been through routing and /or final inspection today.
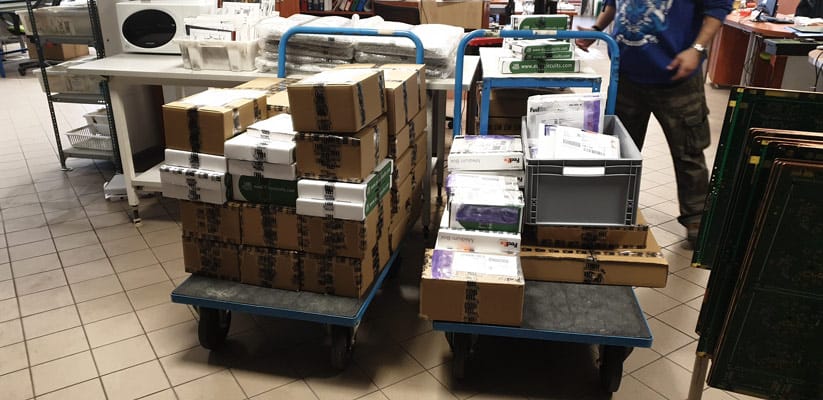
28/10/21 @ 13:00 – Great News!!!
The routing depart is up and running, PCBs that were in this department have been routed, inspected and are ready for shipment to the customer or have been transferred to our assembly facility to begin the assembly process.
28/10/21 @ 12:30 – The cleaning continues
First with the floors so we can walk around without recontamination of the areas already cleaned. Now we start cleaning a part of the walls and the process equipment.
Target is to get the full process up and running ASAP.
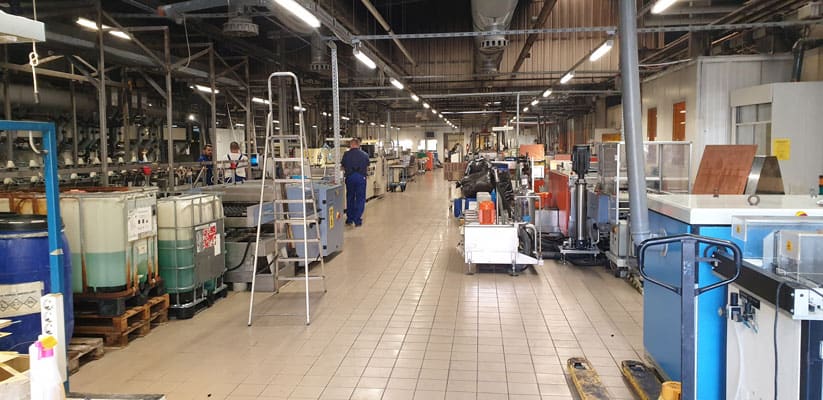
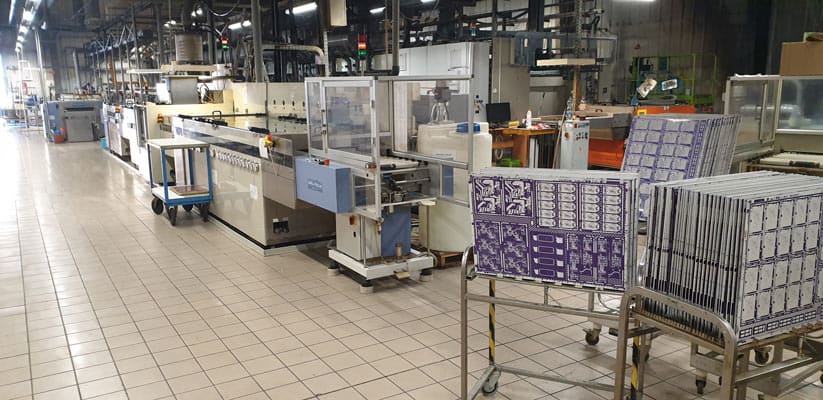
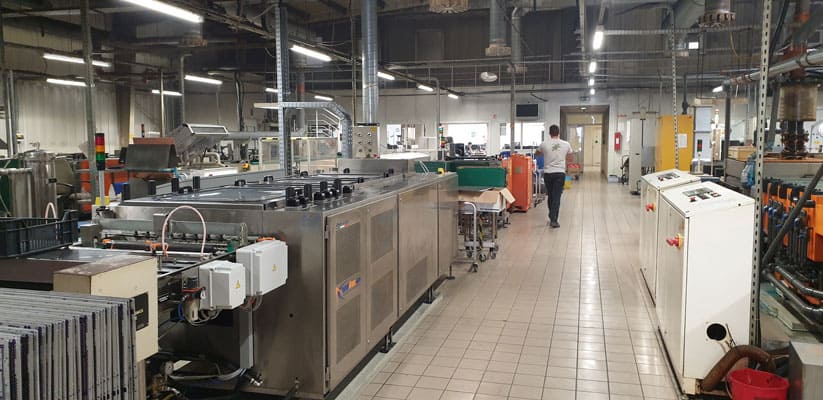
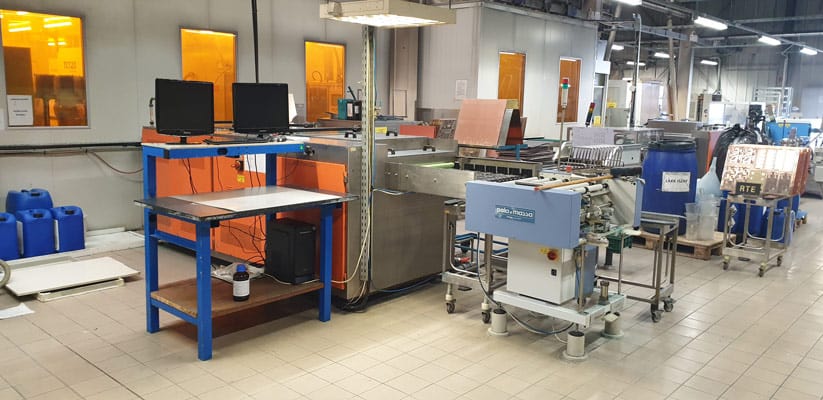
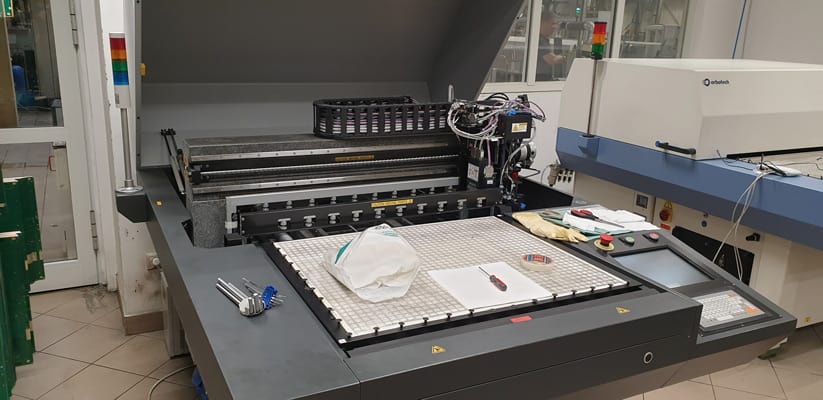
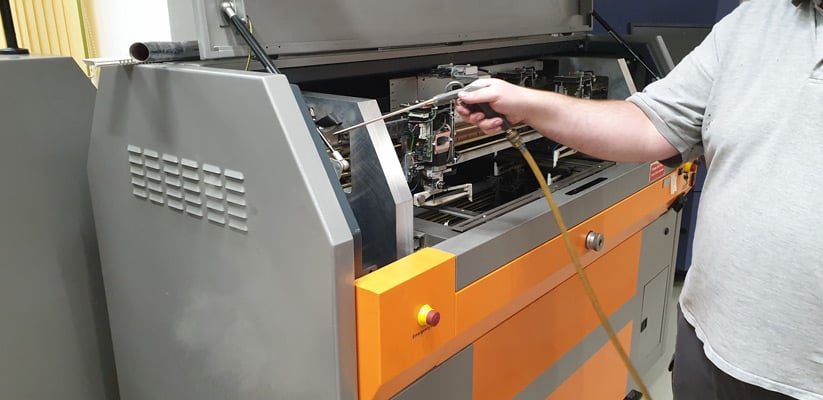
28/10/21 @ 12:00 – Fire damaged equipment
The fire hit hard on some machines that are total loss:
- Both HAL machines and their preparation lines.
- Our hard gold finger line.
- Some chamber ovens.
- Surrounding small equipment of that area.
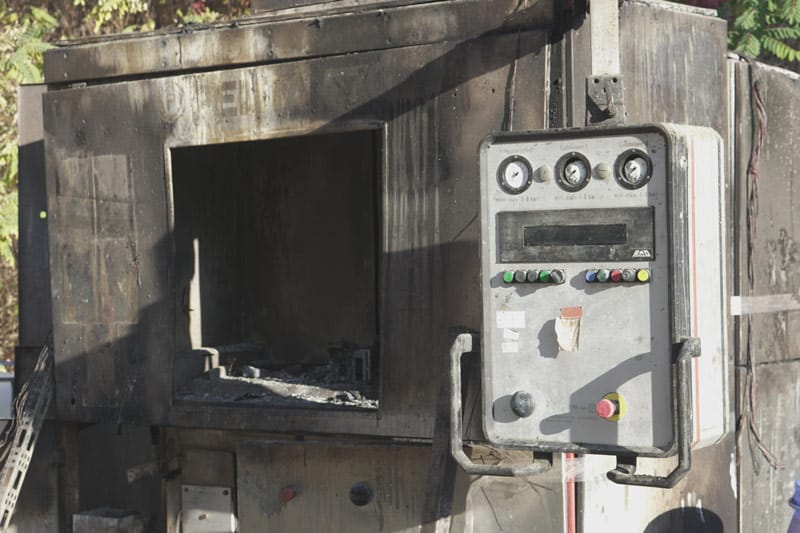
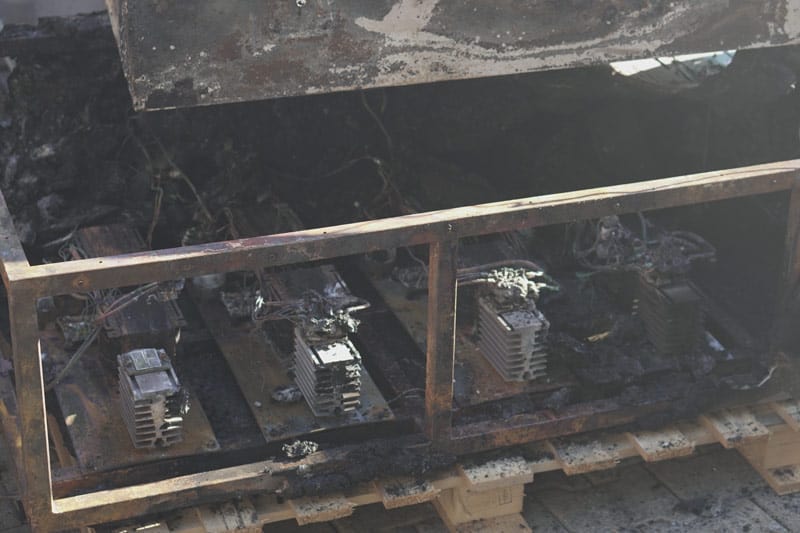
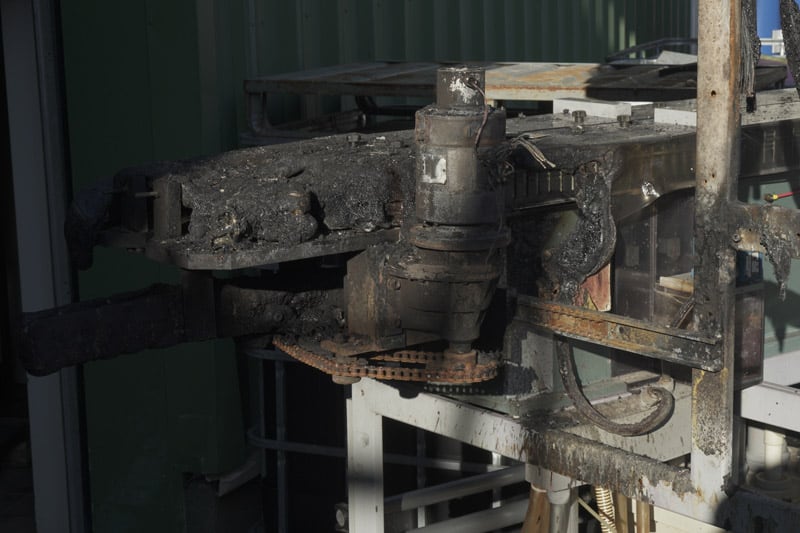
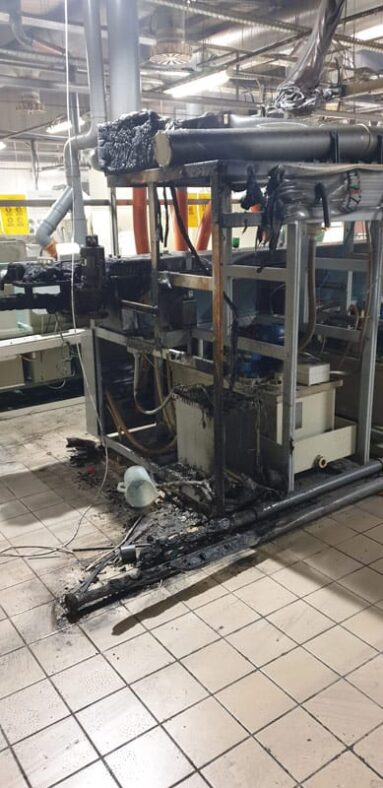
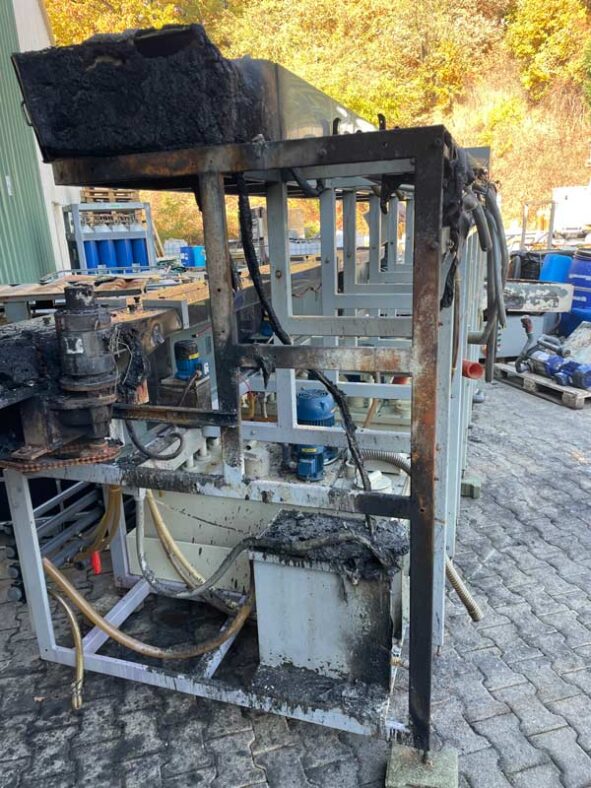
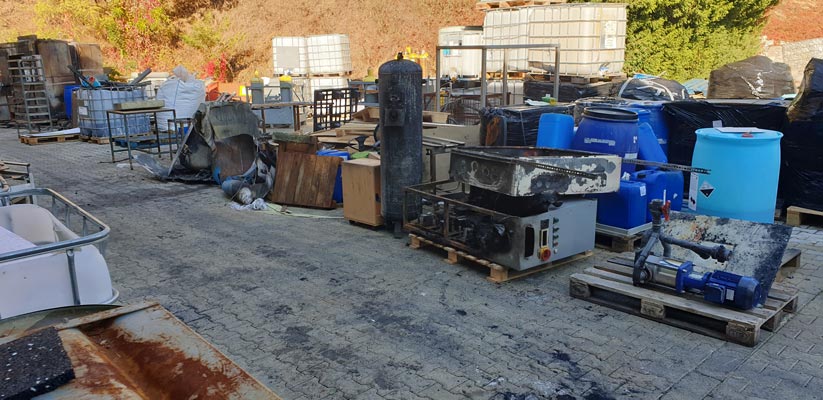
Some delicate equipment suffered soot and water damage and needs further specialist investigation from our suppliers as does the ventilation and air conditioning installation.
28/10/21 @ 10:00 – The cleaning has not stopped since yesterday and continues with the first positive effects on our operation
- The preparation department that prepares all production data for both our production facilities (Eger, Hungary and Aachen, Germany) is fully operational again since this morning.
- The planning department is operational again and is currently busy planning the fastest way to deliver the current orders to our customers.
In the meantime, the cleaning continues. We are cleaning from the end to the start of the production flow. We must clean each machine to remove soot and any water that may have seeped in.
By working this way, we will be able to deliver current orders that are at the end of the process within a reasonable period of time.
Later today or tomorrow, we will notify those customers whose orders may be delayed. We ask for your understanding that this will take some time given the large number of orders still in production.
27/10/2021 @ 22:30 – Our truly committed Staff working into the night
They found and transferred all orders that had passed the final PCB inspection to our assembly facility to start the assembly process.
27/10/2021 @ 22:00 – Our assembly department, which was not directly affected by the fire as it houses in the building next door, started producing again
During the day the power was brought back online (bit by bit) over the entire manufacturing site (2 buildings). With the power now fully restored and the servers and network available again, the assembly building, equipment and team are now fully operational.
27/10/2021 @ 16:00 – Our ICT team managed to get the server and parts of the network functioning again
27/10/2021 @ 14:00 – The Clean up Begins
Around this time the government social services department allowed general access to the building. Rather than sit down and mourn, our people pick up brooms & sweepers and start to refurbish their work environment.
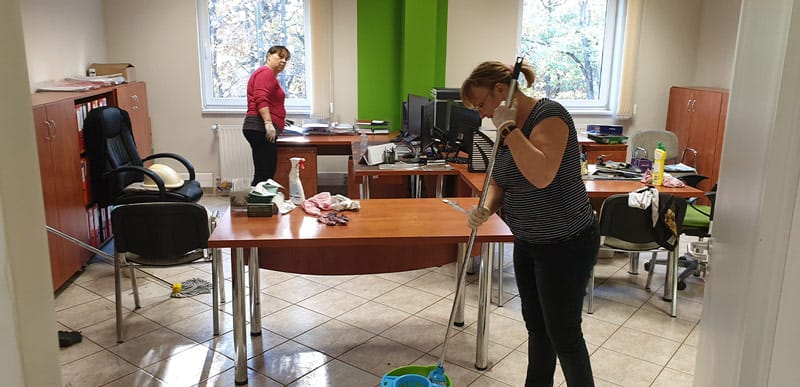
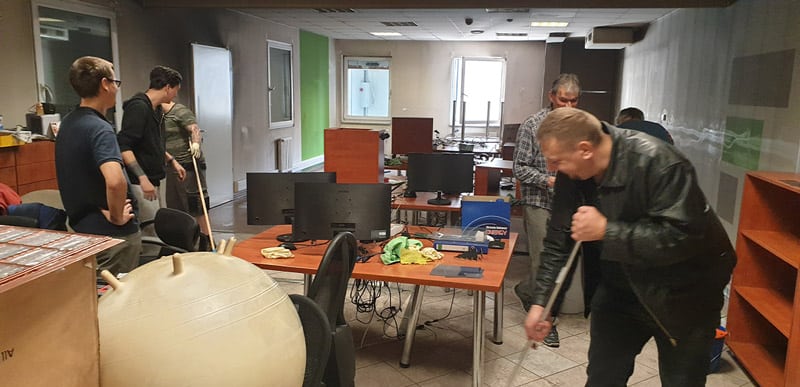
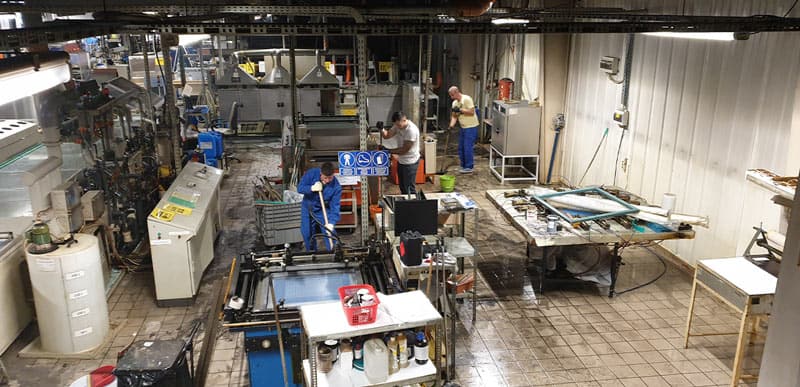
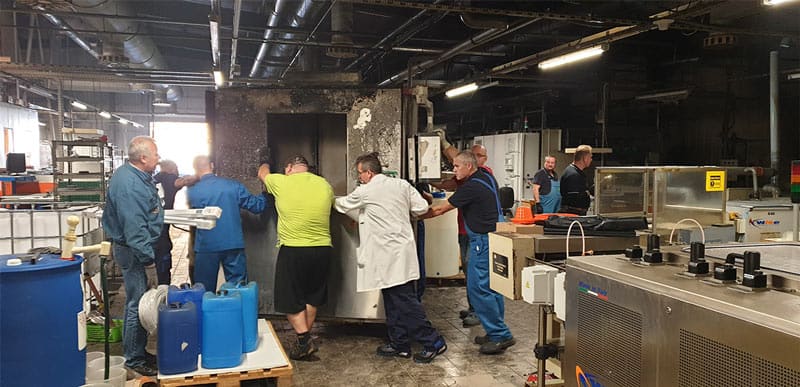
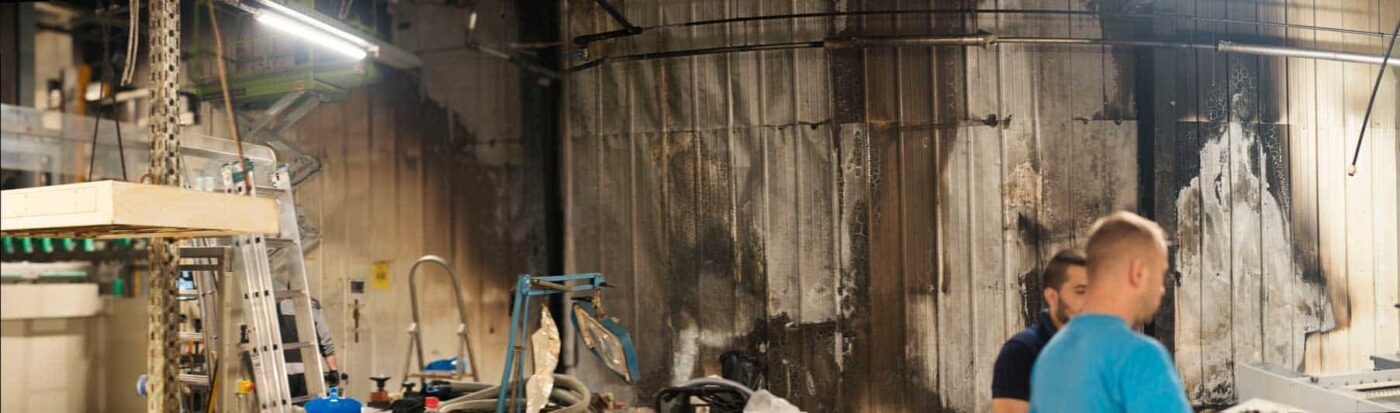
27/10/2021 @ 11:00 – Action taken
Part of the management team was sent to town to buy as many vacuum cleaners for dust and water as they could find, hair dryers were also on the shopping list. This to be able to start any cleaning action as soon as the building is fully cleared for entering.
27/10/2021 @ 10:30 – First Photos from the inside
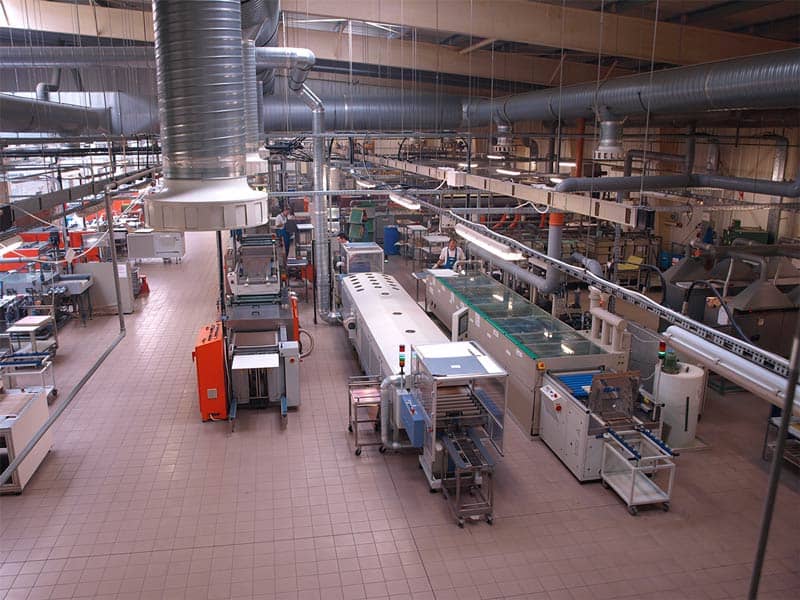
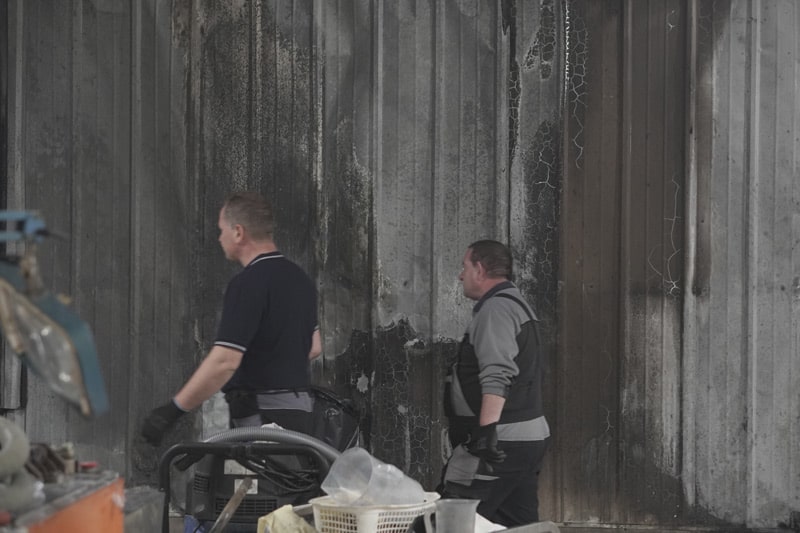
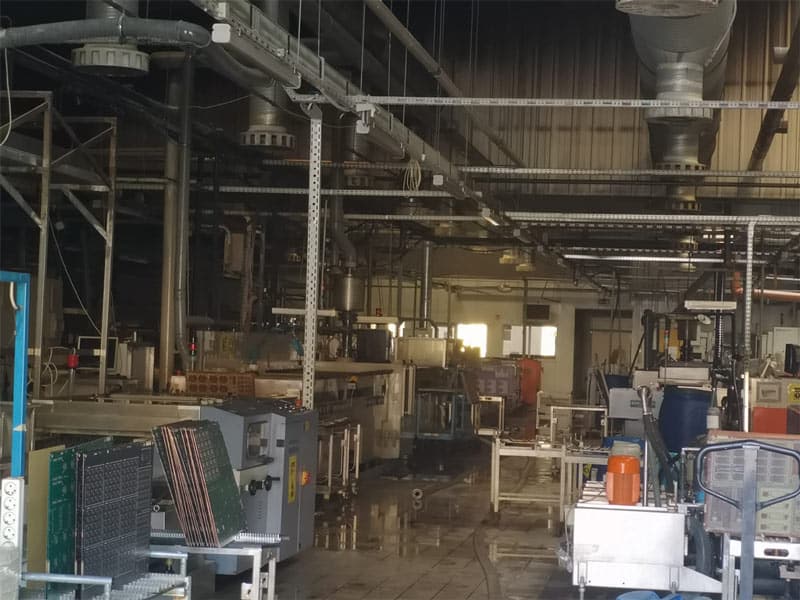
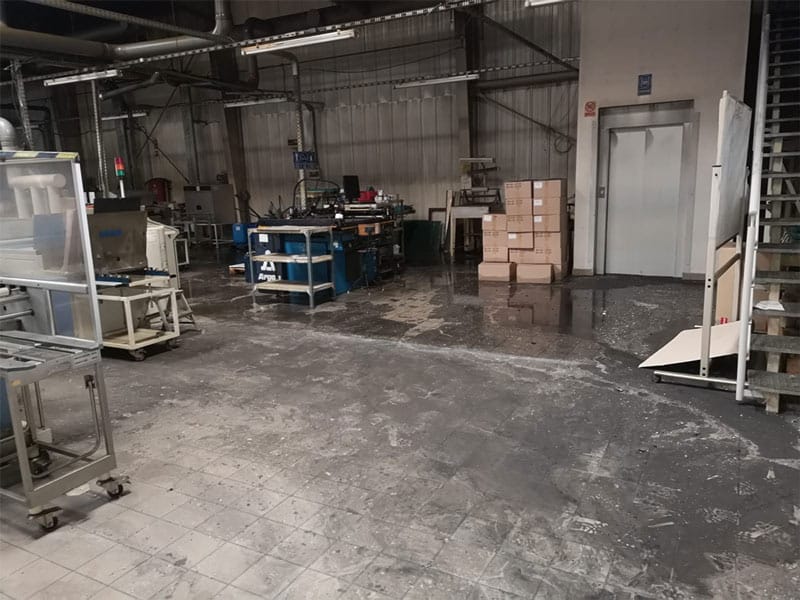
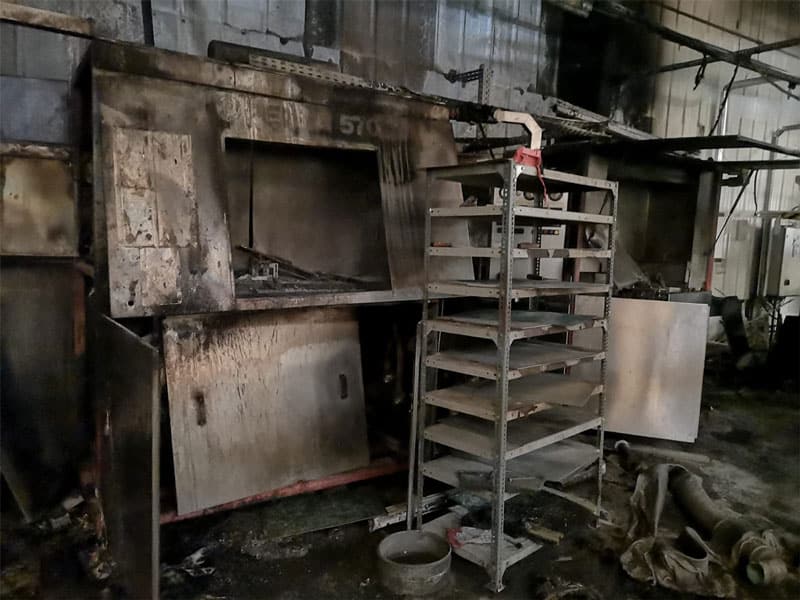
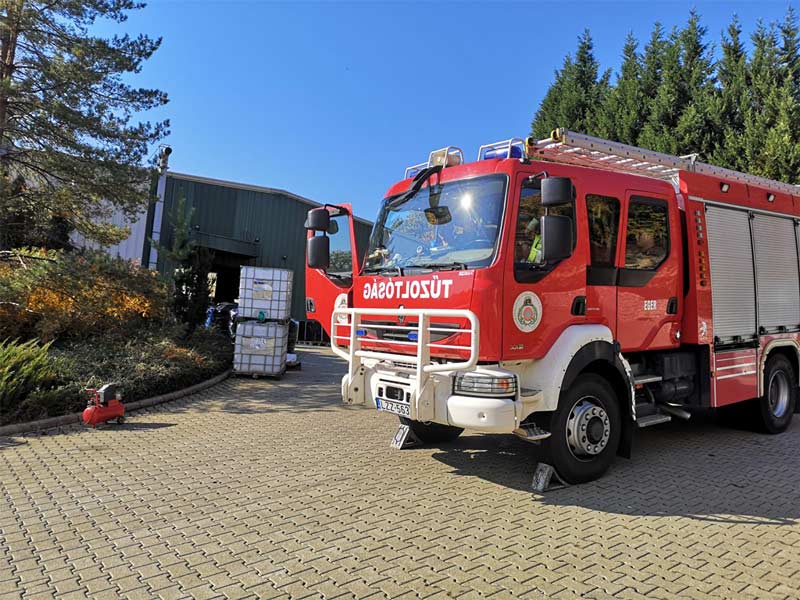
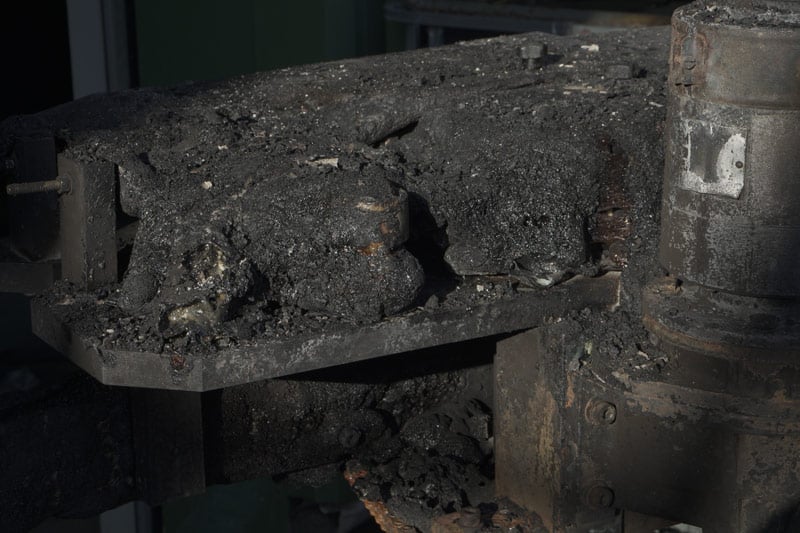
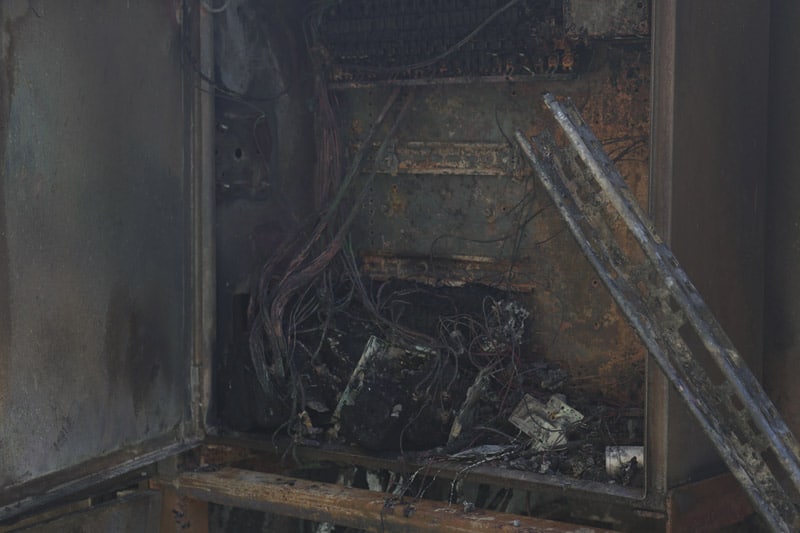
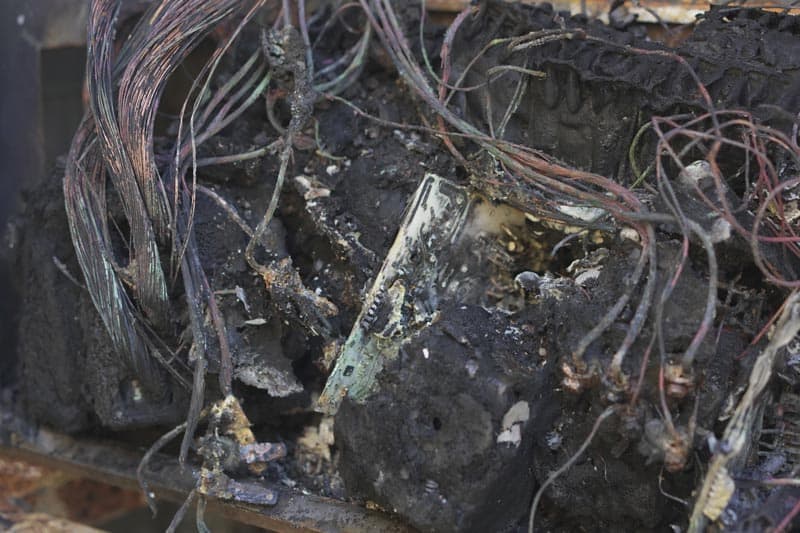
27/10/2021 @ 10:10 – After the Fire Captain allowed limited access, our management entered the building and are currently assessing the damage
27/10/2021 @ 10:00 – Our online tools remain fully at your disposal, but solely relying on our Aachen factory
We can ONLY accept orders for our PCB proto service with a 5 working days lead time, and for our STANDARD pool with a 7 working days lead time, and a maximum order size of 50 pieces and up to 4-layers, with the pooling options that we can manufacture in our German factory.
27/10/2021 @ 01:00 – Firefighters in action
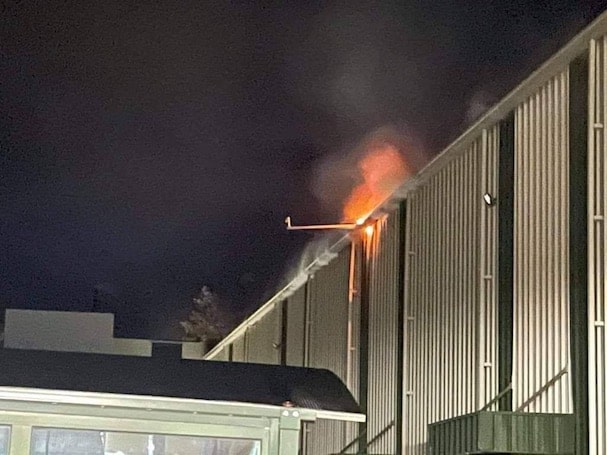
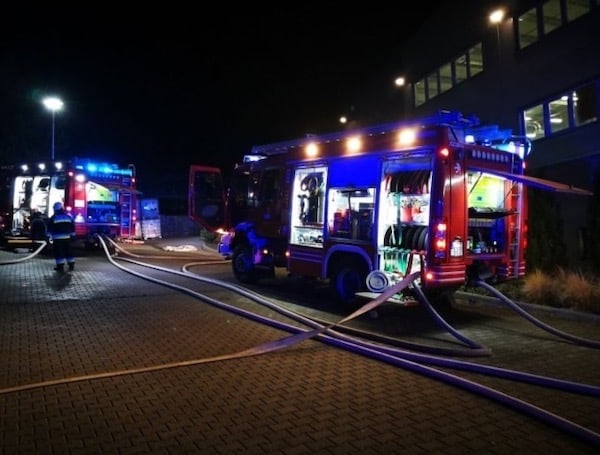
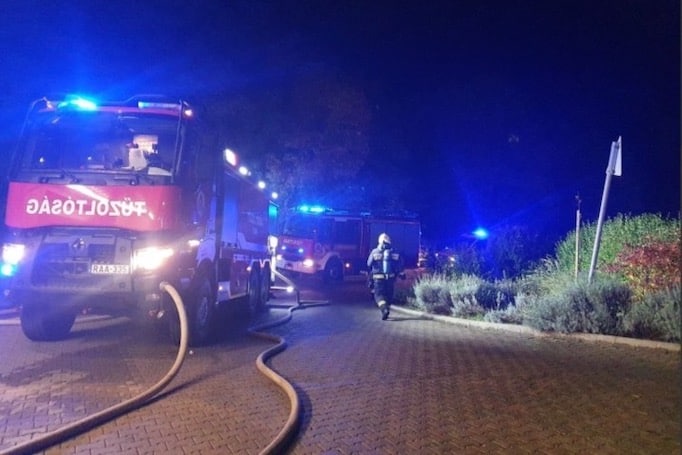