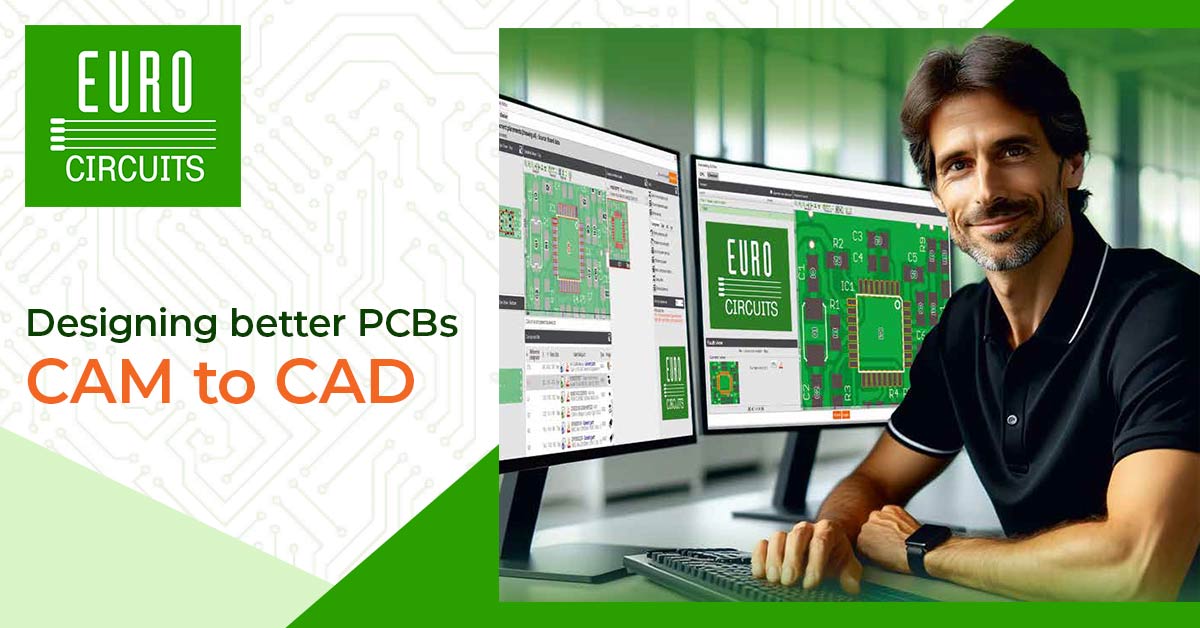
Designing better PCBs: CAM-CAD communication
Speaking the same language is important for communication, obviously, and is particularly so when talking about technical data for manufacturing. PCB data files are generated using CAD – Computer-Aided Design – software that are then sent to a manufacturer, who processes them with CAM – Computer-Aided Manufacturing – software so it’s ready for manufacturing. (CAD […]